Precision Aircraft Parts
We Design State-of-the-Art Precision Aircraft Parts
Matrix Composites specializes in composite design and systems engineering of precision composite structures manufactured using the resin transfer molding process. Our team of experienced engineers is educated in the latest materials, resins, and processes to achieve the desired goal of the composite component.
We are proficient in the conversion from other materials to composites and help our customers develop and value-engineer the best manufacturing process to reduce cost and increase performance.
Applications requiring exacting tolerances, very specific strength and stiffness characteristics or critical physical properties are routinely supported by our engineering staff.
Engineering Excellence
Matrix Composites has a strong M&P engineering heritage and an understanding of robust manufacturing processes.
Design and Development
The U.S. military has developed an advanced artillery system that utilizes composite nose cones as radomes. Matrix Composites was tasked with the development, design, finite element analysis, tooling, and processing of this advanced composite component.
Composite Manufacturing, Tooling Design & Fabrication
Composite Tooling & Fabrication for State-of-the-Art Precision Aircraft Parts
Matrix Composites utilizes a wide variety of composite tooling in the manufacture of precision composites. From CNC machined metal to short-run, low-cost composite fabrication, Matrix Composites can effectively accommodate all of your composite manufacturing needs. We have developed a very high level of confidence in several sources for subcontract CNC machining. These resources, combined with our in-house tool and pattern-making capabilities, assure minimum risk, exceptional tool quality, and mission success.
- Composite, Steel, Aluminum, RTV, and Integrally Heated Tools
- Autoclave
- Vacuum-Bag
- Open Molding Tools
- Precision Fixtures
- High-Temperature Capability
- Dimensional Stability
Personalized Tooling Guidance
Our experts will recommend the best tooling material and design to fit your specific production scenario, whether it is a cost-effective solution for short-run production or durable investments that produce high-quality parts for hundreds of cycles.
Long-term Strategic Alliances
Matrix Composites has long-term strategic alliances with numerous tooling and machining subcontractors. Our trusted partners have a comprehensive knowledge of commercial and military aerospace expectations, which allows for reduced costs and improved performance for our customers.
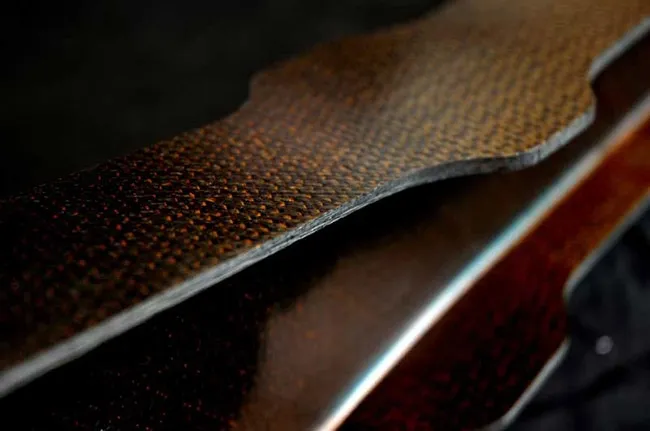
Compression and Composites Resin Molding Experts
Proven Design Methods, High-Quality Products, Compression Molding
Our proven design features, material combinations, composite tooling methods (such as closed molding), and compression molding processes help us conquer the most difficult product design and development challenges.
We are proficient in the conversion from other manufacturing materials to composites. We help our customers develop and value-engineer the best manufacturing process to reduce cost and increase performance for their specific applications.
We've spent years perfecting our various manufacturing, engineering, testing methods, and compression molding processes. Put our extensive composite manufacturing experience to work for you.
Our Composite Process:
- RTM (Resin Transfer Molding)
- HiRPM® (Hot Isostatic Resin Pressure Molding)
- Compression Molding
- Bladder Molding
- Precision Lay-Up/Autoclave Curing
Additional Services:
- Precision Assembly
- Hardware Installation
- Painting
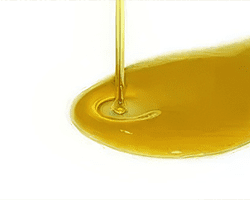
Resin Matrices:
- Epoxy
- BMI
- Cyanate Ester
- Benzoxazine
- Thermoplastics
- Polyimide
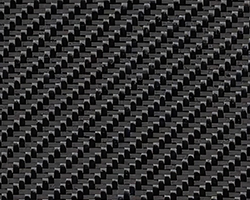
Fiber Types:
- E&S Glass
- Aramid
- Carbon
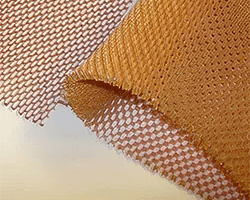
Cores:
- Nomex Honeycomb
- Aluminum Honeycomb
- Rohacell Foam
- Urethane
- Syntactics
Composite Lay-Up Manufacturing Processes
Precision composites manufacturing at our 29,000-square-foot plant
Matrix Composites' 29,000-square-foot manufacturing plant is perfectly suited to meet the precision requirements of aerospace, medical, military, and commercial industries. Our AS9100 quality standards facility is well-equipped to support all phases of composite manufacturing and includes:
- Fabric Pre-Forming
- Advanced Composite Lay-Up
- Segregated Clean Rooms
- RTM Stations
- Autoclaves
- Computer Controlled Ovens
- Heated Platen Presses
- Bonding Areas
- Material Storage
We invest in our manufacturing facilities to keep them state-of-the-art
Matrix Composites continued investment in our manufacturing facilities allows us to offer the highest quality fabricated composite details and assemblies, built to the most demanding specifications.
A range of composite manufacturing processes are performed for prototype and high-volume production at Matrix Composites. Materials and processes conform to "build-to-print" specifications or are specially developed to suit new product requirements.
Secondary Operations
- Trimming
- Drilling
- Painting
- Bonding
- Assembly
- Integrations
RTM Workstations
Matrix Composites has numerous RTM workstations with portable DAQ, injection, and heat (oil or electric).
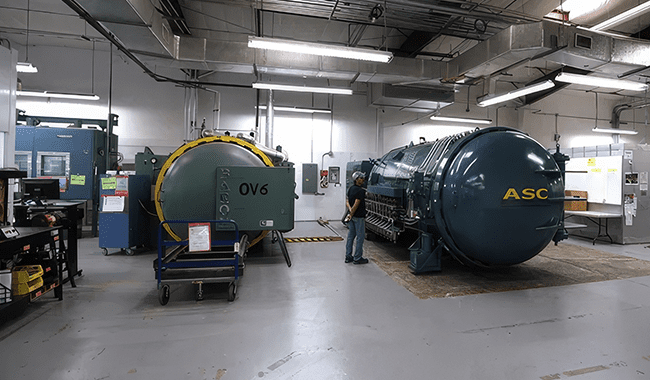
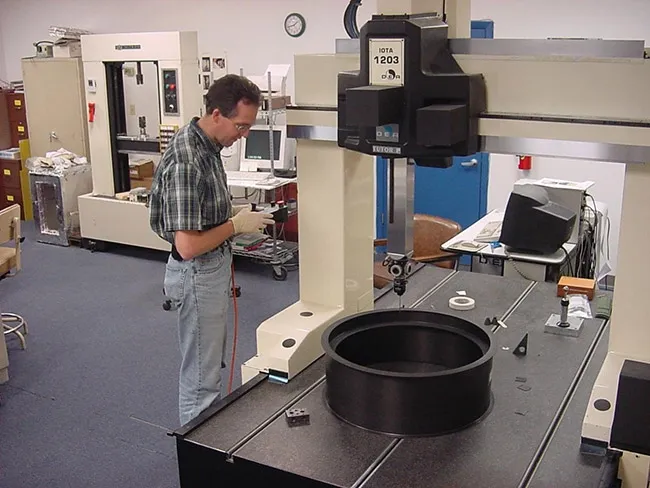
Composites Engineers, Testing, Inspection & Product Verification
Matrix Composites offers comprehensive composite testing capabilities for advanced composite laminates, sandwich panels, structures, adhesives, and pre-impregnated materials. Our staff consists of well-qualified test technicians and composites engineers with extensive experience in the design, fabrication, and testing of high-performance composite laminates.
Our primary objective is to provide rapid turnaround on routine material acceptance and process verification testing, as well as qualified management of more extensive qualification testing programs.
Comprehensive Testing Capabilities
Testing to ASTM, MIL, FED, SACMA, and customer requirements.
Mechanical and Physical Testing
Matrix Composites performs in-house testing for composite laminates, prepreg, adhesives, honeycomb, foam core & sandwich panels.